Feedstock Specifications: Ensures that metal powders are purchased according to strict quality specifications.
DIN EN ISO/ASTM 52904:2019
Additive manufacturing - Process characteristics and performance - Practice for metal powder bed fusion process to meet critical applications
90
5
This standard provides recommendation for the operation and production control of metal powder bed fusion (PBF) machines and processes appropriate in areas of critical applications. A critical application can be assumed once failing parts-functionality leads to immediate threats. The requirements contained herein are applicable for production components and mechanical test specimens using powder bed fusion (PBF) with both laser and electron beams.
Value of Implementation
The ISO-ASTM DIS 52904 standard provides comprehensive guidelines for the operation and production control of metal powder bed fusion (PBF) machines and processes, specifically for critical applications. Critical applications are those where the failure of parts can lead to immediate threats. This standard is applicable to both laser and electron beam PBF processes used in producing components and mechanical test specimens.
Implementing this standard ensures that manufacturers adhere to rigorous quality requirements, enhancing the reliability and performance of PBF-produced parts. Key aspects covered include:
- Personnel Requirements: Ensuring that operators are qualified according to specific standards.
- Digital Data Management: Maintaining accurate records of all digital data used in the production process.
- Equipment Requirements: Specifying the necessary conditions for PBF equipment, including build platforms, shielding gases, and recoater blades.
- Feedstock Control: Establishing guidelines for purchasing, storing, and using metal powders.
- Qualification Procedures: Defining the steps for machine, process, and part qualification to ensure consistent quality.
- Manufacturing Plan and Documentation: Outlining the need for a detailed manufacturing plan and proper documentation throughout the production process
By following these guidelines, manufacturers can achieve higher consistency, traceability, and quality in their PBF processes, ultimately leading to safer and more reliable products for critical applications.
User Benefits
Supply Chain Manager
Quality/Production Engineer
Process/Operation Engineer
Correlation to ISO/ASTM 52920:2023
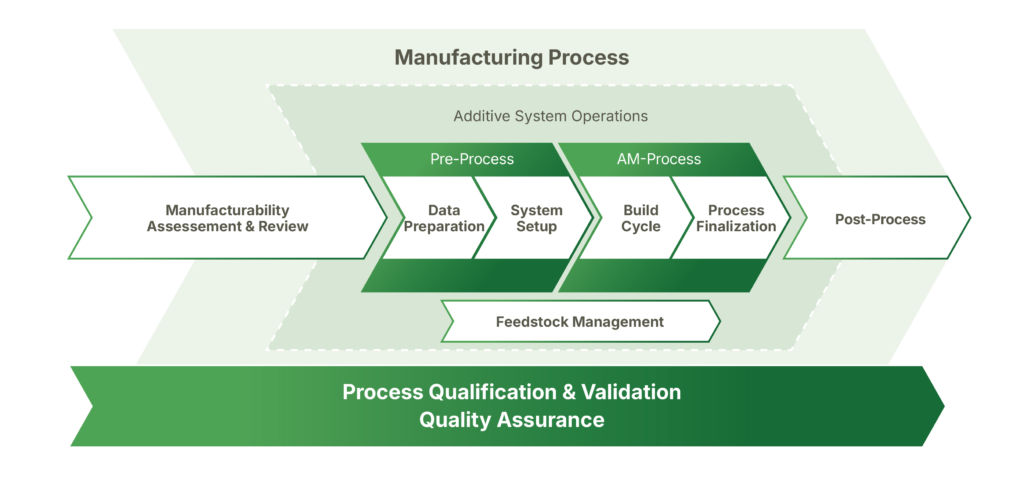
Supplier related with DIN EN ISO/ASTM 52904:2019
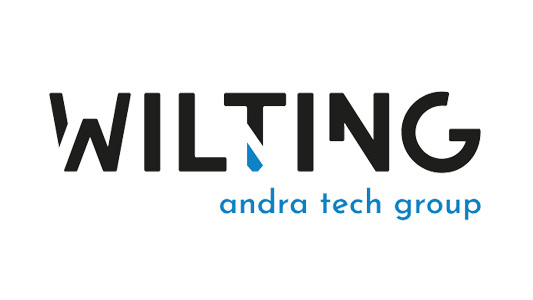
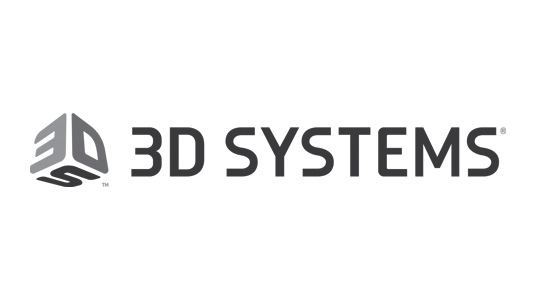
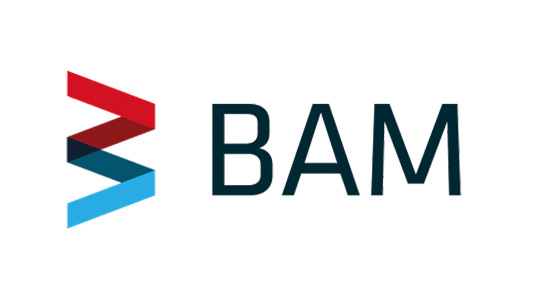
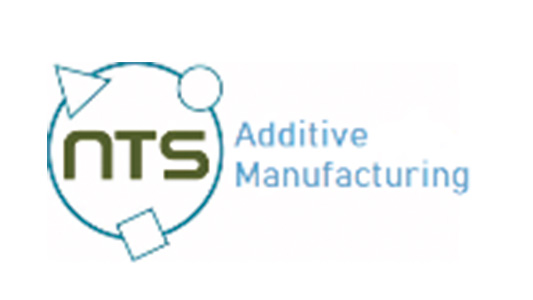
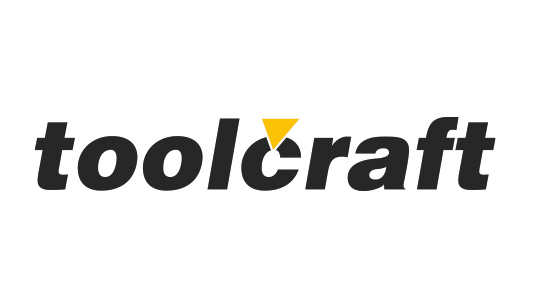